As an effective means of energy conservation, the lightweight technology of heavy trucks has become one of the important research topics in the development of the automobile industry. The lightweight of heavy trucks is an urgent need to improve the competitiveness of automobiles, and it is also an urgent need for the national energy conservation and emission reduction strategy. With the rapid development of the logistics and transportation industry, the lightweight of trucks has become the main trend of the development of the global truck manufacturing industry, and lightweight automotive material technology has become one of the important standards for the research and development of new trucks.
Lightweight heavy trucks involve complex system engineering in many aspects such as technology, economy, safety, and environment, including a series of key supporting technologies such as parts optimization design and testing technology, advanced manufacturing technology, material recycling and regeneration technology, and parts maintenance technology. The late development of my country’s automobile industry, small and scattered production scale, weak R&D capabilities, and shortage of R&D talents have restricted the rapid development of my country’s heavy truck lightweight technology.
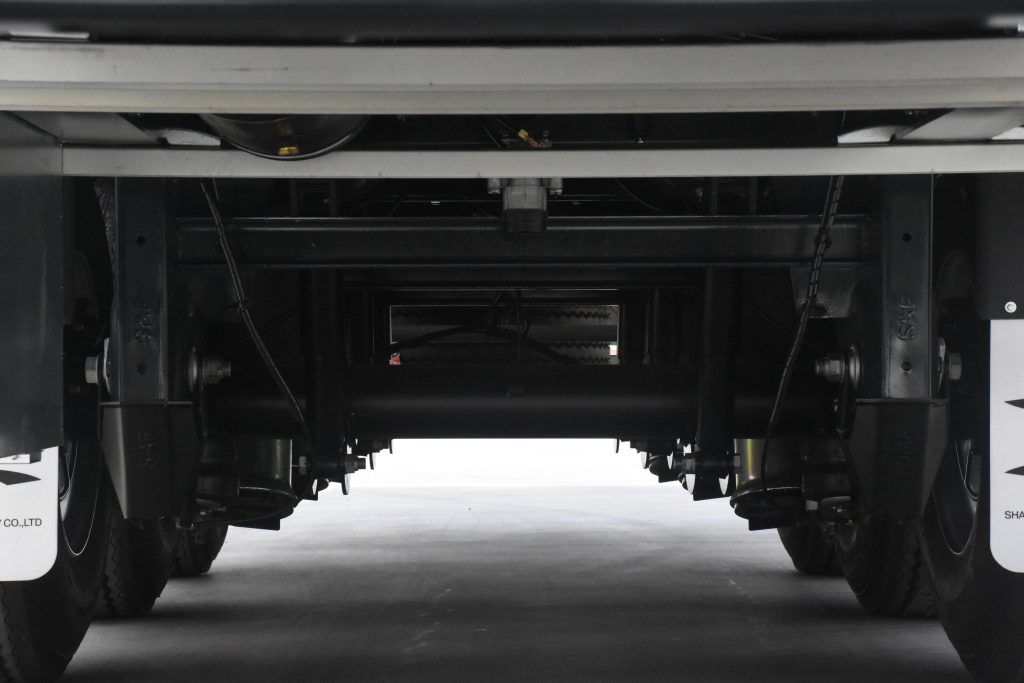
Due to the demand for lightweight R&D, body weight reduction design and the use of new materials have become one of the key technologies to reduce fuel consumption, taking the application of aluminum alloy materials in automobile manufacturing as an example. If the design is appropriate, aluminum can be used instead of steel, and every time the weight of the body is reduced by 10%, 6 to 8 percent of gasoline can be saved. Aluminum truck transportation can effectively increase the load capacity, reduce the frequency of transportation, reduce fuel consumption when empty, save fuel, have strong anti-oxidation ability, and the service life of the whole vehicle can reach 15-20 years.
The lightweighting of trucks is a cumbersome and complex system engineering, involving tractors, engines, carriages, beams, etc. In Europe and the United States, the development and application of aluminum semi-trailers in developed countries has a history of more than 30 years, and the technology is quite mature. Although my country is the world’s largest aluminum producer and consumer, the proportion of aluminum used in the transportation field is only 18%, and the development of aluminum semi-trailers is still in its infancy.
Compared with the common heavy-duty truck lightweighting technology in China, an all-aluminum semi-trailer can reduce weight by 3.4 tons, save 45,000 liters of fuel during its life cycle, and reduce carbon dioxide emissions by 110 tons. At present, there are 1.1 million heavy-duty semi-trailers in my country. If 80% of them can be all-aluminum vehicles, with an annual driving distance of 150,000 kilometers, 5.31 million tons of fuel can be saved annually. With a service life of 800,000 kilometers, about 28.35 million tons of fuel can be saved annually. At the same time, carbon dioxide emissions can be reduced by about 90 million tons. It is reported that aluminum trucks mainly serve the logistics and transportation industry. Economic growth has an increasing demand for logistics. The logistics industry will have a broad development prospect in 3-5 years.
For China’s automobile industry to become bigger and stronger and actively participate in international competition, independent research and development, breaking through technical bottlenecks, and mastering core technologies are the only way. All related industries, including the steel industry, need to work together to establish a cooperative mechanism for joint participation. The truck industry alliance is a beneficial attempt. Only by integrating resources, giving play to the advantages of “joint forces”, and making key breakthroughs can my country’s truck industry transform to a high-performance, low-energy, and low-emission model.