Mining vehicles are off-road vehicles, mainly used in mines and engineering. They are more durable and carry more than general trucks. From a structural point of view, there seems to be no big difference between mining vehicles and ordinary dump trucks, as if they are just a little “bigger”. In fact, mining vehicles are essentially different from ordinary dump trucks in terms of design concept. Ordinary dump trucks are used to meet the needs of road transportation, while mining vehicles are used to meet the needs of mine construction. Therefore, the entire vehicle and the parts used in mining vehicles take into account the mining operating environment and are designed and manufactured for such users.
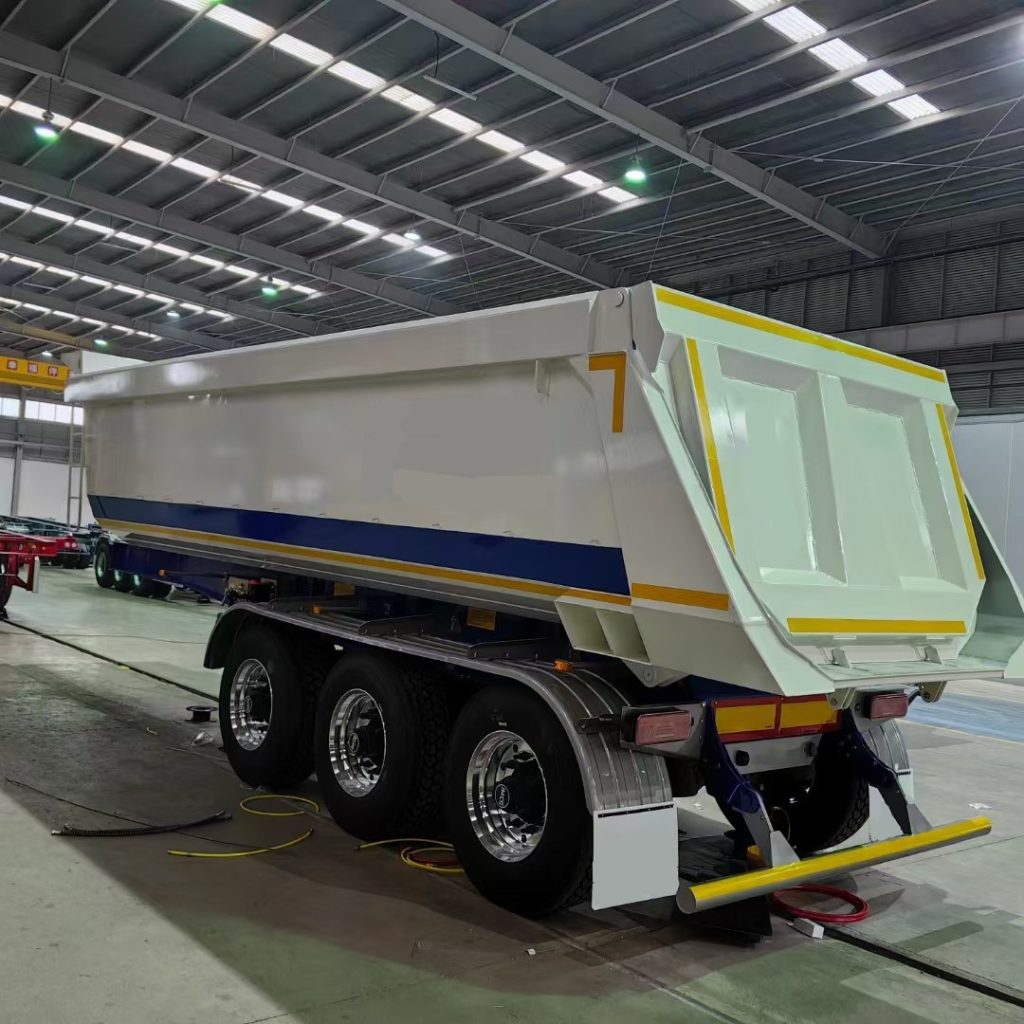
Characteristics and structural features
Off-road (mining) dump trucks are heavy-duty dump trucks used in open-pit mines to complete rock and earth stripping and ore transportation tasks. Their working characteristics are short travel distance and heavy load. They are often loaded with large electric shovels or hydraulic shovels, and travel back and forth between mining sites and unloading sites. The “off-road” here does not mean off-road driving, but it is not allowed to drive on the road because of its super-wide appearance and excessive total mass. Rigid frame dump trucks are widely used in my country. The following briefly describes their characteristics and structural features:
(1) The appearance is particularly tall and belongs to the super-profile vehicle
Mining dump trucks are only driven within a limited mining area. The vehicle’s external dimensions are not restricted. In order to increase the transportation volume of each trip, the volume of the carriage is increased as much as possible, and the overall dimensions of the vehicle are widened and heightened. Its width far exceeds the national JTGB01-2003 “Highway Engineering Technical Standards” and GB1589-2004 “Road Vehicle External Dimensions, Axle Load and Mass Limits” that the width of road vehicles shall not exceed the limit of 2.5 meters, and cannot be driven on the road.
(2) Large load mass and strong power
At present, the load mass of this type of vehicle is between 20-360 tons, and it is also developing in the direction of large-scale. Due to the large load tonnage and the slope of the road, the engine must have high power and high torque to ensure that it is easy and powerful when fully loaded uphill. Therefore, this type of vehicle is equipped with an engineering engine with high “specific torque” and high “torque increase coefficient”. However, due to the poor off-road conditions, the common speed of this type of vehicle is around 30-40km/h.
(3) 2-axle type
The wheelbase and total length are shortened. The loading and unloading area of the mining area is small, and there are frequent turns and reversing. The roads in the mining area are mostly temporary roads. There are many ups and downs in the mountainous area and many sharp turns. In order to maintain maneuverability and flexibility, the wheelbase and total length are shortened to reduce the turning radius and reduce the number of reversing. Therefore, the 2-axle 4×2 structure is basically adopted to ensure a simple chassis structure, convenient maintenance, and sensitive steering. For such vehicles, their single-axle load far exceeds the single-axle load limit of 12 tons specified in GB1589-2004 “Road Vehicle Outline Dimensions, Axle Load and Mass Limits”, and they cannot be driven on the road.
(4) Frame
The frame is a special structure for engineering machinery vehicles. It is a fully welded structure. Its longitudinal beam adopts a closed box section to ensure high torsional strength. The thick steel plates used are all low-alloy, high-strength steel plates.
(5) Carriage
The carriage is also a fully welded structure, with a bucket-shaped floor that is tilted at the rear, generally with a slope angle of 12 degrees, and no rear guardrail; the floor is welded from high-strength, high-hardness, impact-resistant high-quality steel plates to adapt to the harsh off-road industrial and mining transportation and the rough stone loading method on engineering sites, and its service life is generally guaranteed to reach more than 10 years.
(6) Suspension
Most off-road (mining) dump trucks use oil-gas suspension, especially those with a load capacity of more than 45 tons. This type of vehicle with a short wheelbase and particularly large mass is most suitable for installing oil-gas suspension. It does not have the corresponding space to install traditional leaf spring shock absorbers. The oil-gas spring cylinder of its front wheel also serves as the steering kingpin, and the outer cylinder is fastened to the outside of the frame longitudinal beam, thus eliminating the traditional integral front axle.
(7) Steering
Due to the large mass of the vehicle and the large load on the front axle, the steering of the front wheel relies entirely on hydraulic power. To ensure safe and reliable steering, this type of vehicle not only uses full hydraulic steering, but is also equipped with an emergency steering system. When the steering system power fails, the emergency steering system can ensure that it still has a certain steering ability and stop the vehicle in a safer place.
(8) Braking
The mining area is sloped and the vehicle load is particularly large. Therefore, the reliability of the braking system function also needs to be guaranteed first. In addition to the main brake function of the dump truck, it is also equipped with auxiliary retarding braking capabilities: engine exhaust braking, hydraulic retarder or electric retarder function of the electric wheel converted into a generator. The braking function is designed with advanced design. When braking starts, the engine exhaust brake is put into operation first; then the hydraulic retarder or electric retarder jointly joins the retarding braking function; finally, the wheel main brake is put into operation again, which greatly reduces the frequency of use of the main brake, often in the best condition, and the service life of the brake shoe is extended.
(9) Transmission
Vehicles with a load capacity of less than 100 tons generally use a hydraulic mechanical transmission and a traditional rear axle; large vehicles with a load capacity of more than 100 tons generally use electric transmission: the engine drives the generator, which then uses the current to drive the electric motor in the rear wheel, so that the rear wheel drives the car.
(10) Use of engineering tires
The tread pattern and structure of the tires of this type of vehicle are different from those of road vehicles. They are engineering tires that are well adapted to the use requirements of complex roads.