1.The connection between the supercharger and the intake and exhaust pipes of the Flatbed trailer transporter must be tight and leak-free. If there is leakage between the exhaust pipe and the exhaust turbine, the efficiency of the supercharger will be greatly reduced, the exhaust temperature of the diesel engine will rise sharply and damage the valve and supercharger.
2.Before starting a new engine, the supercharger and supercharger oil filter must be filled with clean oil to ensure that the supercharger bearings can be lubricated as soon as the diesel engine starts.
3.Before the diesel engine is shut down, the flatbed transporter should be operated at idle speed for 3-5 minutes to reduce the speed and temperature of the supercharger, and monitor the sound of the supercharger operation. If any abnormality is found, the engine should be stopped for inspection. If the supercharger rotor is not flexible and there is a jamming or wear sound, it must be sent to a qualified maintenance station for repair.
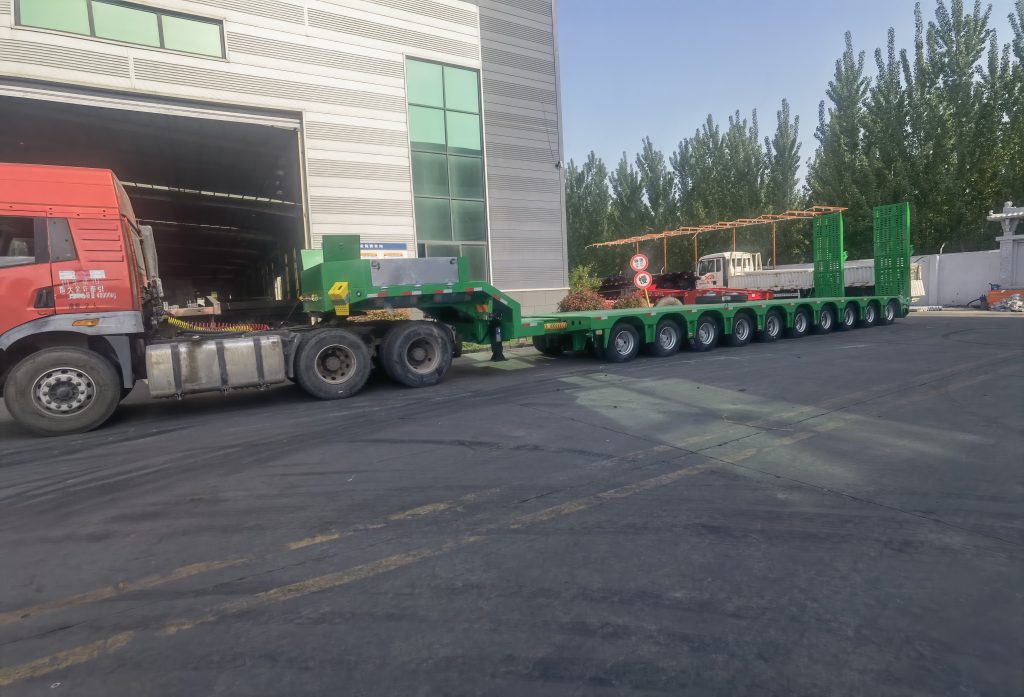
4.For flatbed transporters, the clearance on the supercharger rotor shaft should be checked after every 500 hours or 30,000 km of operation, and dust and carbon deposits on the compressor turbine shell and rotor blades should be removed. At this time, the turbocharger should be removed from the diesel engine and the metal gasket between the supercharger exhaust pipes should be replaced. Mechanical methods are not allowed to remove the deposits on the rotor components, but gasoline or other detergents for cleaning aluminum parts should be used.
5.The locking nut of the turbocharger compressor on the flatbed transporter cannot be disassembled, otherwise the dynamic balance of the turbocharger rotor will be destroyed, causing damage to the turbocharger.
6.Do not damage or deform any rotating parts of the removed turbocharger, otherwise it will affect the balance of the turbine. Also, do not damage any rubber seals.
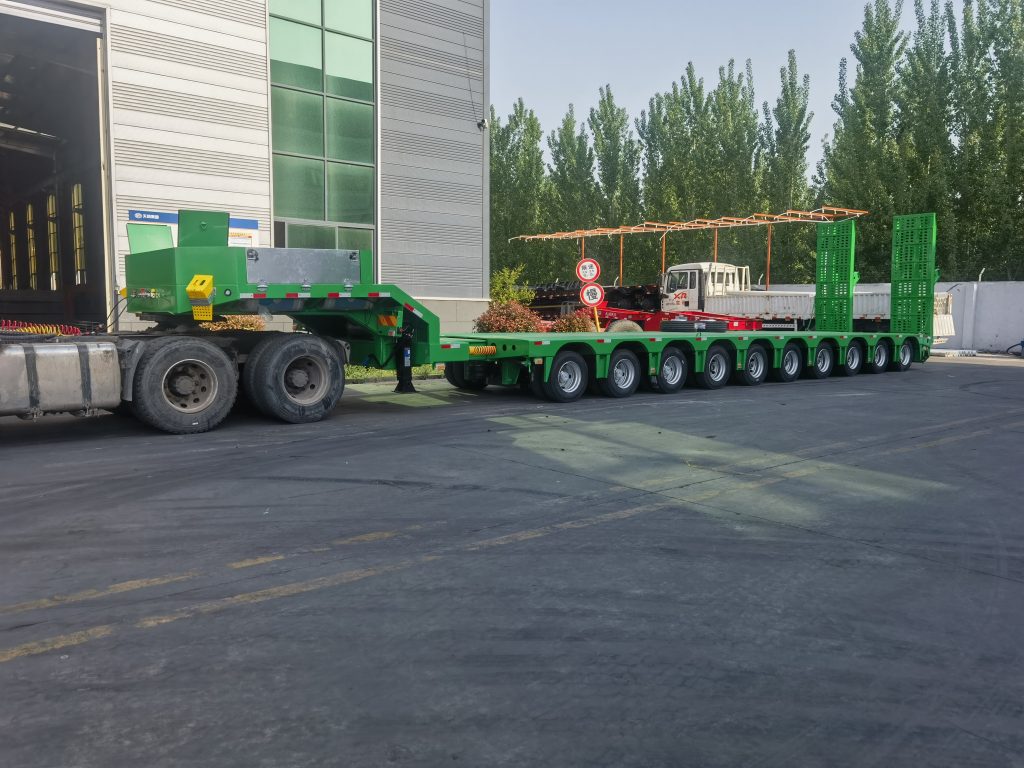